PLANT BLOG
What Is Prefab?
A Deep Dive Into Prefab Construction
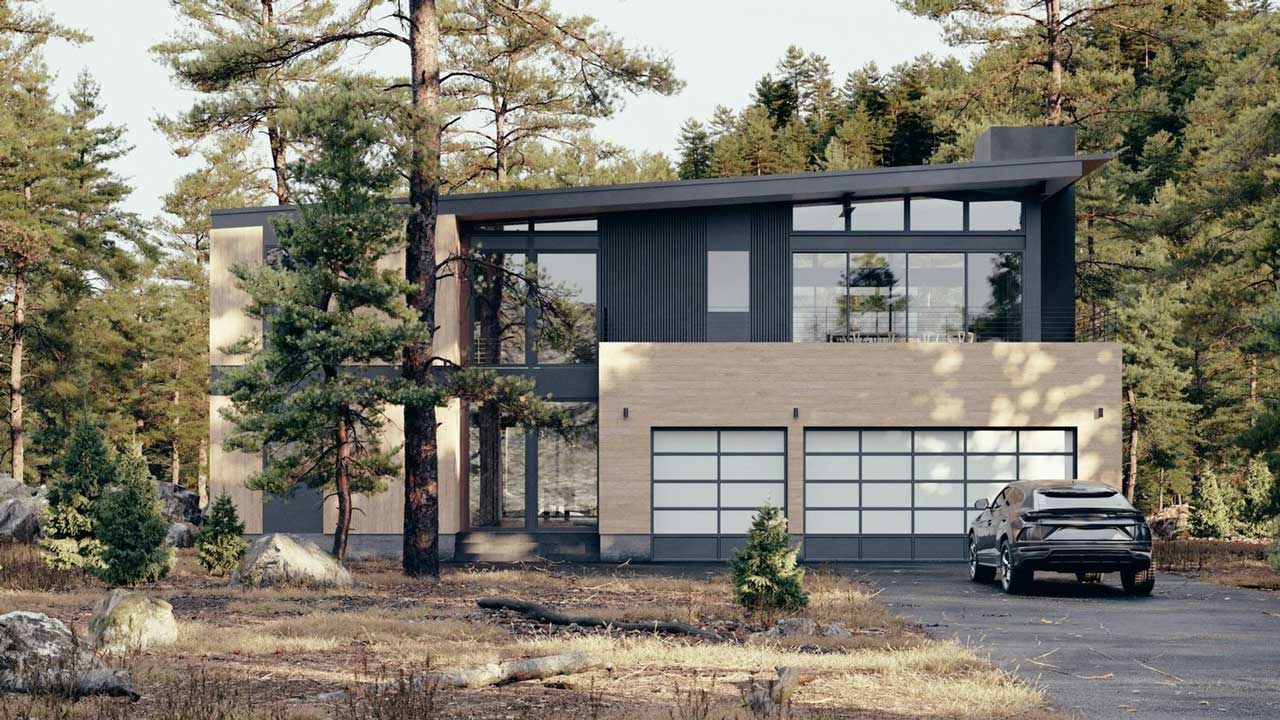
Custom single-family prefab home designed by Ray Kappe and prefabricated by Plant Prefab.
With its reputation as a modern, sustainable way to build, prefabricated construction, or prefab, has experienced significant growth in recent years with widespread coverage in the media.
Despite this rise in recognition, prefab construction remains misunderstood by many, likely because it’s used for so many different applications. From backyard accessory dwelling units (ADUs), tiny homes, and cabins, to multi-floor, multi-unit housing and hospitality developments, this highly efficient and reliable method of building is being utilized in many forms across both residential and commercial construction.
Here at Plant Prefab, we prefabricate housing so that’s what we will focus on as we explain this method of construction.
What is a Prefab Home?
At its most basic, a prefab home is one that was constructed off-site, typically in a factory, and then brought to and assembled on a prepared building site. This contrasts with traditional “stick-built” construction in which a home is built entirely on-site. Prefab homes can be built in a variety of ways, which we explain below.
History of Prefab
While prefabricated homes have existed in some form or another for centuries, the modern concept of prefab took shape within the United States in the mid-1800s during the California gold rush. At that time, the population of California was growing so quickly that few homes were available for the state’s new residents. To meet the huge demand, houses were built back east and then shipped on trains to San Francisco, Sacramento, and other rapidly growing towns.
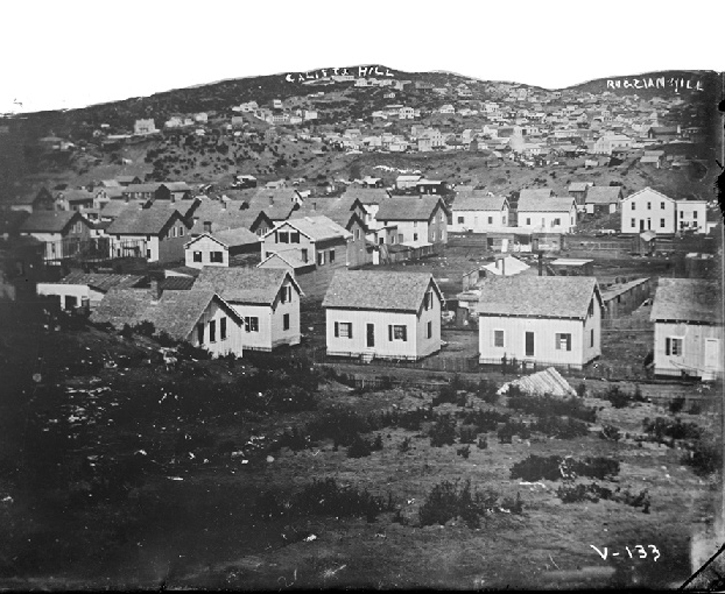
Prefab homes in San Francisco, 1850, Credit: OpenSFHistory / wnp71.0521.
In the early 1900s, Sears & Roebuck popularized the concept of “kit” homes. Conveniently ordered out of a Sears catalog, each kit included the plans for a home, as well as all of the parts, which were shipped to the buyer for on-site assembly. Available in a variety of sizes and price points and facilitating fast and simple construction, these homes made the dream of homeownership a reality for many Americans—over 70,000 of these Sears homes were built between 1908 and 1940.
In the 1940s, after World War II, the United States encountered a huge housing shortage due to wartime building restrictions, later compounded by the return of over 7,000,0000 soldiers from overseas at the war’s end. In response, numerous aluminum and steel companies, newly in search of profitable opportunities, attempted to meet demand by building prefabricated metal homes. These companies found little success due to high fixed factory costs and the challenges of building standardized, non-custom homes that could still meet building codes that varied from place to place.
In 1974, the government addressed these regional code challenges by introducing a new federal code for manufactured and mobile housing, regulated by the Department of Housing and Urban Development. As a result, mobile homes grew dramatically in popularity, providing a low-cost housing option for people across the country. Unfortunately, the proliferation of this type of inexpensive and generally low-quality prefab housing caused many to equate prefab with mobile homes, a negative association that continues today.
Types of Prefab Homes
Manufactured Homes
Also known as mobile homes, manufactured homes are constructed entirely off-site and delivered complete. The important distinction to understand about manufactured homes is that they are built according to federal building code governed by the Department of Housing and Urban Development (HUD), which is far less stringent than the state, regional, and local building codes that govern the construction of other types of prefab and site-built housing. As such, they are typically much lower quality and less expensive than other types of prefab housing.
Modular Homes
Modular homes are constructed in large segments, called modules, in a factory and then assembled on-site. Modular-built homes follow the same stringent state, regional, and local building codes as site-built homes, requiring higher-quality construction than manufactured homes.
Modular construction can achieve significant time and cost savings over site-built construction, but shipping large modules becomes expensive over long distances, so construction cost savings diminish with shipping distance. Also, not every design can be built as large modules, and not every job site can accommodate the huge trucks and cranes required to deliver and install large modules.
Panelized Homes
Panelized homes are constructed using factory-built floor, wall, and roof panels that are assembled and finished on-site according to state, regional, and local building codes. Because panels are generally much smaller than modules, they can be used to construct more complex designs. They can also pack flat and ship on smaller trucks, facilitating access to urban infill lots and other challenging lot shapes and locations.
However, standard panel products require a great deal of skilled labor hours on the jobsite to assemble, wire, plumb, and finish. This makes panelized construction only moderately more time- and cost-efficient than site-built construction.
Plant Building System™
The Plant Building System is a hybrid methodology that utilizes specialized panels and modules developed by Plant. Improving upon existing panelized products, which only incorporate framing and insulation, Plant Panels™ can also include plumbing, electrical, and finish materials.
Plant Panels can be used on their own, assembled into “core” Plant Modules™ for kitchens, baths, or mechanical rooms, or built into fully-volumetric Plant Modules that comprise entire rooms or sections of a home.
This flexibility achieves the benefits of modular and panelized building methods, making the Plant Building System an ideal solution for urban infill, projects with challenging lot shapes, and the construction of any architectural design across any housing typology, from single family homes and multi-family housing, to hospitality, healthcare, and student housing.
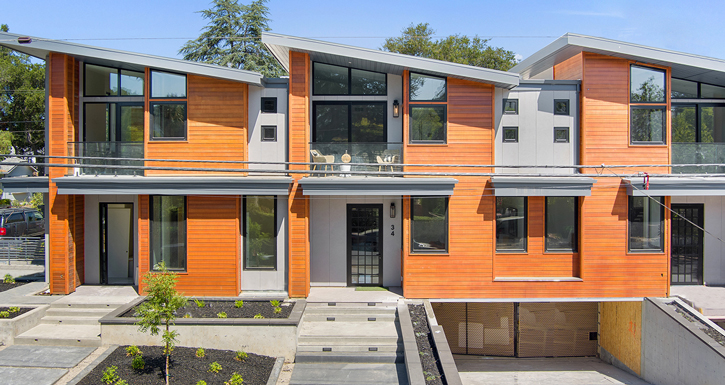
Custom townhomes designed by Metro Design Group and prefabricated by Plant Prefab using the Plant Building System™
The Future of Prefab Housing
In 2023, Plant Prefab will open a 270,000-square-foot automated production hub that will build prefab housing with even greater speed and precision than our existing facilities.
With a crippling housing shortage throughout the United States, exacerbated by a dearth of skilled labor and supply chain disruptions, the construction industry is increasingly looking to prefab as a solution, and prefabricators are experimenting with new materials, building techniques, and delivery methods. With market demand and investor interest both on the rise, we predict a very bright future for the prefabrication industry—and we look forward to continuing to lead the way.
Ready to get started on the prefab home of your dreams? Take the next step:
- Discover how our architectural design studio can support your project
- Contact us today
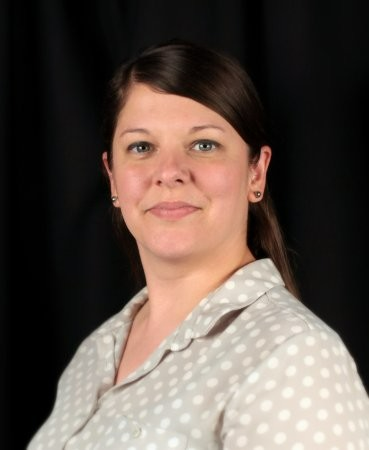
ABOUT THE AUTHOR
Jeanne Haegele is Plant Prefabs's Marketing Content Developer, working to share Plant's story and explain the benefits of prefabricated construction.
Contact Us
Learn how Plant can help you build a higher-quality home, faster and more efficiently than any other builder.
Join Our Newsletter
Sign up for our monthly newsletter to receive new posts, news, and more.
LEARNING CENTERLearning Center